Utilizing a network of sensors and cloud software, Internet of Things technologies can collect critical production data and give companies valuable insights into the efficiency of manufacturing operations. This enables manufacturers to improve productivity and enhance manufacturing and supply chain operations.
Key Takeaways:
- IoT in manufacturing offers significant benefits: cost reduction, faster market time, improved decision-making, mass customization, and safety improvements.
- IoT technologies enhance shop floor operations, supply chain management, and remote operations.
- Challenges in IoT adoption include data security, investment needs, employee qualifications, and technology integration.
Read on to learn more about how IoT is transforming the manufacturing industry.
5 Benefits of IoT in Manufacturing.
There are five primary benefits to implementing IoT solutions in manufacturing:
- Cost reduction.
- Reduced time to market.
- Improved decision making.
- Mass customization.
- Safety improvements.
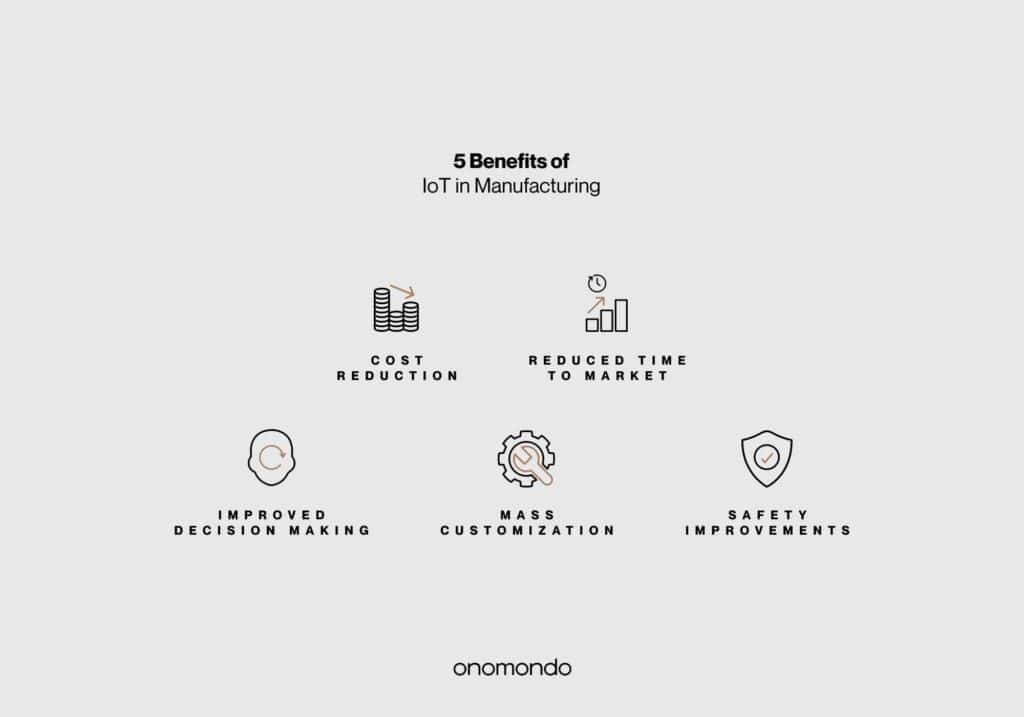
1. Cost reduction.
In manufacturing, the most significant expenses companies face are energy, materials, and losses caused by downtime.
IoT makes it possible for manufacturers to reduce operational costs and create new sources of revenue by:
- Optimizing asset management and inventory management.
- Reducing machine downtime.
- Enabling more agile operations and more efficient energy use.
Along with asset and inventory management, predictive maintenance enables companies to eliminate possible issues and avoid unforeseen expenses associated with sudden repairs.
2. Reduced time to market.
IoT in manufacturing plays a notable role in reducing the time that passes from the conception of a product until that product is released to the market. This is made possible through:
- Faster and more efficient manufacturing and supply chain operations.
- Direct communication between employees and network components.
- Faster decision making and improved response to market fluctuations.
These benefits allow products to quickly move from concept to commercialization, reducing product cycle time and thus contributing to significant time savings.
3. Improved decision making.
As mentioned above, IoT solutions for manufacturing facilitate faster decision-making. This is because resource management and asset optimization involving both humans and machines depend on comprehensive data.
With IoT technology, manufacturers can:
- Gather valuable data and distribute it through robust networks in real time.
- Ensure fast information flow throughout the manufacturing facility.
- Gain valuable insights into the performance of their systems and devices.
These benefits enable managers to continually create dashboard metrics that help broadcast results and lead to faster, more informed decision making.
4. Mass customization.
The manufacturing industry is seeing an increasing demand for mass customization – a process which requires a significant increase in the variety of stock-keeping units (SKUs) produced.
IoT facilitates mass customization by:
- Eliminating latency through real-time information sharing between every element in the supply chain.
- Allowing buyers to select their desired components with ease.
- Suppliers and logistics providers see the exact components ordered and adjust their schedules accordingly.
In this way, the real-time data provided by IoT enables thoughtful forecasting, shop floor scheduling, and data routing.
5. Safety improvements.
The Internet of Things can help to ensure a safer working environment in the manufacturing industry. IoT makes it possible to:
- Monitor the physical health of workers through wearable IoT devices.
- Indoor proximity systems for adhering to COVID-19 social distancing measures.
- Detect risky activities that can result in injuries.
- Address safety problems in potentially hazardous environments.
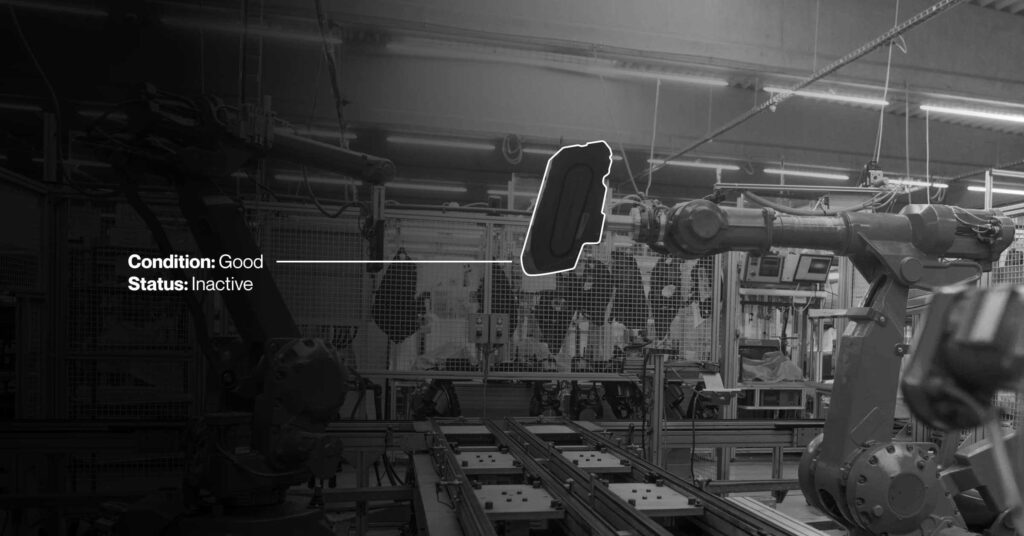
For example, IoT solutions can detect gas leakages by monitoring the level of harmful emissions in the environment, helping to prevent unsafe working conditions, and reduce the number of accidents in the facility.
The 3 dimensions of IoT’s impact on manufacturing.
The impact of the Internet of Things on the manufacturing industry is notable. IoT technologies are transforming the way production systems are built and run.
This digital transformation is particularly tangible within the following three dimensions:
- Shop floor and field operations.
- Manufacturing supply chain.
- Remote and outsourced operations.
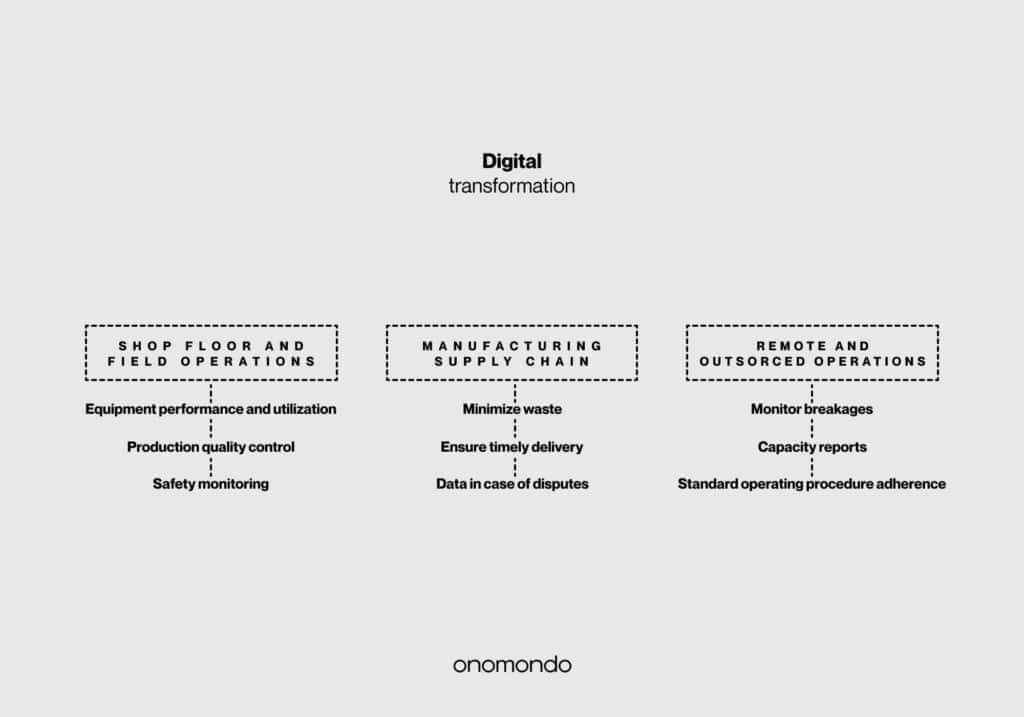
Dimension 1: Shop floor and field operations.
IoT in manufacturing offers an advanced level of visibility into shop floor and field operations, while also enabling greater control over company resources.
Manufacturing execution systems (MES) and systems for enterprise resource planning (ERP), which are commonly used in manufacturing, are unable to work with detailed information such as the location of items in the inventory or real-time equipment status records. IoT technologies, however, are able to meet demands which MES and ERP systems cannot.
IoT provides manufacturers with real-time shop floor data. This makes it possible for businesses to significantly increase the productivity of their manufacturing processes. The IoT applications that increase manufacturers’ visibility fall into two categories:
- Applications which support manufacturing operations.
- Applications that facilitate industrial asset management.
Manufacturing operations driven by IoT.
IoT-driven manufacturing operations monitor and optimize:
- Equipment performance and utilization.
- Production quality control.
- Safety monitoring.
According to McKinsey, the manufacturing improvements which IoT applications drive could be worth more than $470 billion per year by 2025.
Equipment performance and utilization.
IoT solutions for monitoring and optimizing equipment performance and utilization provide businesses with real-time metrics that offer a detailed view of what happens during every step of the production process.
Performance and utilization monitoring begins with extracting data concerning machine operating parameters. Among others, these parameters include run time, operating speed, and product output, and are extracted from sensors, supervisory control and data acquisition systems (SCADA), or distributed control systems (DCS).
The collected data is gathered in real time and then transmitted to the cloud for processing. The cloud analyzes the data, turning it into valuable insights into equipment performance and utilization KPIs.
Once the data is analyzed, the factory workers can access the results via a web or mobile app.
Production quality control.
The quality of produced goods can be monitored in two different ways:
- By inspecting work in progress (WIP) products as they move through the production cycle, or
- Through condition monitoring and calibration monitoring of the machines on which products are manufactured.
WIP inspection provides more accurate quality control results, as it makes it possible to uncover inaccuracies in the alignment of parts and other minor defects. However, this method has certain limitations:
- WIP inspection is only applicable to discrete manufacturing – i.e. the manufacturing of finished products that are distinct items capable of being easily counted, touched, or seen.
- Quality control based on WIP inspection requires all WIPs to be inspected manually, making this a time-consuming, labor-intensive, and costly process.
- The WIP inspection method provides only a fractional overview of product quality, as it is rarely possible to inspect every single WIP product.
The condition and calibration monitoring method provides only the binary classifications “good” and “not good” and therefore offers far less differentiation in terms of scope. However, it does enable:
- Detection of bottlenecks in the manufacturing process.
- Identification of underperforming and/or poorly tuned machines.
- Timely prevention of machine damage.
Condition and calibration monitoring also includes parameters such as equipment calibration, machine conditions, and environmental conditions. These parameters are monitored to detect when they cross their recommended thresholds, as this can lead to product defects.
If sensor readings approach these thresholds, a quality monitoring solution will pinpoint the source of the issue, alert users to the issue, and recommend a mitigation action to repair or tune the machine. This minimizes the production of low-quality products, saving time, labor, and expenses.
Safety monitoring.
In industrial sectors such as transportation, mining, and oil & gas, workers are equipped with radio frequency identification (RFID) tags and wearable sensors.
The RFID tags collect data on workers’ locations, and the sensors gather data on parameters such as workers’ heart rate, skin temperature, galvanic skin response, and more. Once collected, the sensor data is relayed to the cloud.
To detect unusual behavior patterns such as unusual heart rates or sudden vertical movements, the data is analyzed against contextual data – e.g., data from environmental sensors, weather feeds, and legacy work planning systems. This helps to prevent work-related injuries from falls, overexertion, overheating, overheating, and more.
Whenever parameters that could pose a risk to workers are detected, a message is automatically sent to the employee’s doctor, manager, or other via a mobile app.
Dimension 2: Manufacturing supply chain.
In the manufacturing industry, IoT-enabled supply chain management solutions are driving productivity and increasing cost efficiency.
At any segment of the manufacturing supply chain, smart supply chain management solutions provide manufacturers with real-time information about every item.
Not only does IoT for manufacturing supply chain optimization keep managers updated on whether a particular SKU is available; it keeps managers informed of the status, location, and condition of each item of that SKU in real time.
IoT solutions in manufacturing prevent the loss of goods.
Before IoT was implemented in manufacturing, condition monitoring of goods during storage and delivery could only be carried out on arrival. Now, goods, components, and materials can be monitored en route, enabling manufacturers to monitor fragile items and perishable goods – e.g. glassware, food, pharmaceuticals – in real time.
This means that if e.g. a pharmaceutical company ships an order to a distribution center via a third-party logistics service provider, IoT sensors are attached to the inside of the pharmaceutical containers to monitor the temperature within.
If the temperature inside the containers begins to rise due to cooling system failure during transport, the following occurs:
- The IoT sensors within the containers detect the temperature rise and register the deviation from the recommended threshold.
- The IoT solution alerts the driver of the cooling system failure. The system also sends a notification to the manufacturer, alerting them that the delivery conditions have been violated.
- The driver resets the cooling system and thus prevents the pharmaceuticals within from being spoiled.
This way, the IoT solution prevents the loss of goods, which:
- Minimizes product waste.
- Ensures timely delivery.
- Helps to prevent disputes between the manufacturer and the delivery company.
- Spares the manufacturer the expense of replacing spoiled goods.
Dimension 3: Remote and outsourced operations.
As mentioned above, there are numerous challenges in the manufacturing industry. These include:
- High logistics costs.
- A greater demand for customization.
- Higher customer expectations.
- An increasingly complex global supply chain.
- Lack of local talent.
These challenges lead manufacturers to outsourcing their talent and distributing their shop floor operations.
Building or buying a manufacturing facility in another city, state, or country means that manufacturers must ensure that the new facility maintains their production and manufacturing standards.
Compliance with production standards must therefore be monitored – and this can be accomplished with IoT.
IoT solutions monitor remote manufacturing operations.
In manufacturing, IoT solutions can optimize everything from production monitoring to machine maintenance.
IoT-based utilization monitoring solutions provide manufacturers with real-time equipment efficiency metrics. This ensures that manufacturers are always up-to-date with production efficiency and eliminates the need for direct access to the shop floor.
IoT-based predictive maintenance enables timely prediction of potential equipment failures. This makes it possible to schedule maintenance activities in advance, eliminating the necessity of keeping a maintenance team on site.
Another example of how IoT facilitates remote operations is through smart connected products (SCPs). SCPs are complex systems comprising:
- Sensors.
- Hardware.
- Cloud software.
- Connectivity.
- Embedded intelligence.
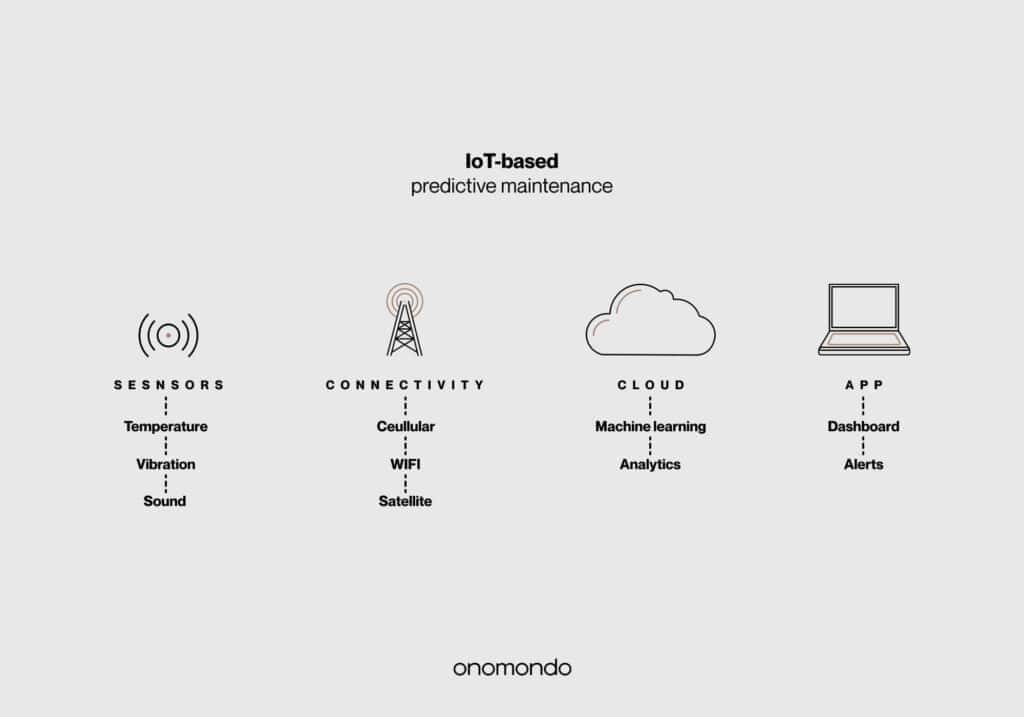
SCPs can exchange data using short-distance transmission via a local network or via the internet.
SCPs enable manufacturers to access real-time data about remote operations. For example, company managers located in California can access real-time data about the operating and condition parameters – such as temperature, vibration, and rotation speed – of the SCPs of their manufacturing affiliate in Texas.
This keeps company managers informed about:
- Breakages.
- Possible overload conditions.
- Violations of the standard operating procedures.
This way, IoT makes it possible for remote operations to run smoothly and allows manufacturers to remain entirely in control of their operations without being on site.
Read more: What are Internet of Things (IoT) devices?
IoT adoption: the challenges of digital transformation.
Despite the magnitude of the potential benefits of implementing Internet of Things technologies in manufacturing, some manufacturers are still holding back from adopting IoT solutions.
The reason for this is that the implementation of IoT in the manufacturing industry is not without its own challenges. The IoT-driven digital transformation of large, mature systems requires time, effort, and resources – no matter the industry.
According to a BCG survey, some of the greatest challenges that US enterprises face when beginning the digital transformation of their operations concern:
- Data security.
- Investment needs and ROI.
- Employee qualifications.
- Technology integration with legacy systems.
Data security.
Without proper security measures, connected devices can be highly vulnerable to cybercrime. Indeed, according to a Netwrix survey, manufacturing was targeted by cyberattacks more often than many other industries in the last twelve months.
This makes it highly important for manufacturers to prioritize implementing efficient protection solutions and to equip legacy systems incorporating IoT technology with defensive tools.
In short, when implementing IoT in manufacturing, a security strategy should be in place from the very beginning.
Investment needs and ROI.
Implementing IoT in manufacturing requires investing in:
- Hardware – e.g. sensors and gateways,
- Connectivity.
- Cloud software.
- Technical support.
- Administrative labor.
There is no way around the fact that IoT initiatives are resource heavy. Before implementing IoT, companies should therefore consider:
- How fast they can roll out new solutions, and
- How quickly a solution will begin to generate revenue.
Employee qualifications.
Managing IoT in manufacturing requires qualified specialists, and the increasing number of smart factories means that the skills gap among employees is growing wider. Many companies also experience a shortage of IoT-experienced workers at management level.
The areas in which employees and managers lack expertise and experience include:
- Analytics.
- Big data.
- Embedded software development.
- Embedded electronics.
- Cybersecurity.
- Artificial intelligence.
This also means that it can be difficult for manufacturing executives to make decisions concerning their solutions due to their lack of knowledge, competencies, and experience with IoT.
To address this issue, employees and managers should receive the right instruction, training, and education in IoT and other relevant technologies from the start.
Technology integration with legacy systems.
One of the greatest challenges of rolling out IoT solutions in manufacturing ecosystems is integrating information technology (IT) and operational technology (OT) without security inconsistencies and data losses.
In the past, IT and OT systems had different objectives and were therefore built based on different networks and technologies. This makes seamless convergence between IT and OT difficult.
Today, the fast diffusion of web-based user interfaces and the rapid adoption of Ethernet protocols at machine level are gradually easing the IoT integration process. However, a true solution to this challenge has yet to be found.
Use the world’s smartest IoT connectivity stack.
Modern enterprises run on data, but only about 15% of the world’s economy is currently digitized. Data is needed for digital transformation to happen at scale, and IoT is the primary way to generate this data.
As described in this article, manufacturing is an industry that stands to make significant gains from IoT.
Connectivity is a vital part of IoT and is currently underutilized. Most see connectivity simply as a way to commute data. But IoT networks can actually take the burden off of devices and:
- Centralize security.
- Unify management.
- Optimize performance.
- Simplify development, deployment, and operation.
Onomondo is the world’s only IoT Connectivity Stack that has deep integrations with over 700 networks worldwide.
Thanks to our Core Network and range of tools available via our API or SIM platform, users can benefit from:
- One SKU/APN.
- One, global connectivity partner.
- Full control and transparency over networks,
- APIs and webhooks that integrate connectivity with their tech stacks, and
- No-code Cloud Connectors which simplify deployments and reduce data consumption.